- Blog
- Comparison of FRP Coating and Traditional Spray Coatings
Comparison of FRP Coating and Traditional Spray Coatings
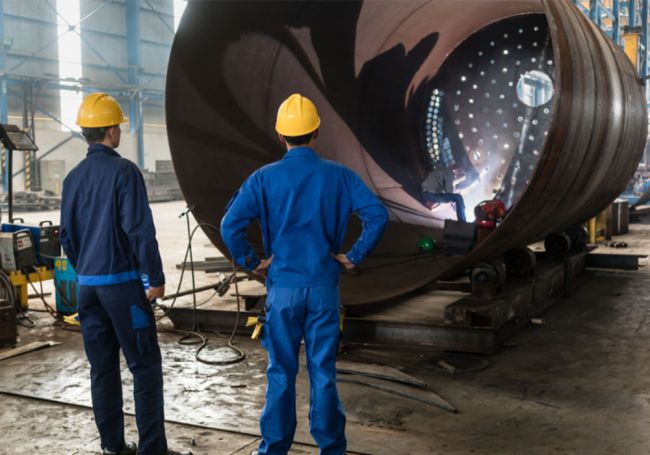
When selecting the ideal coating solution for industrial applications, it is crucial to compare the advantages and disadvantages of different methods. Two popular options are Fiber-Reinforced Polymer (FRP) Coating and Traditional Spray Coatings. Below, we analyze their features to help determine the best choice for various applications.
Foaming Control
FRP coatings utilize vacuum stirring and complete defoaming during production, ensuring a smooth and defect-free application. In contrast, traditional spray coatings rely on artificial defoaming, which often results in incomplete foam removal and compromises coating integrity.
Adhesive Properties
FRP coatings contain epoxy resin, which provides superior adhesion to various surfaces. On the other hand, traditional spray coatings are based on unsaturated polyester, which has weaker adhesion properties, making them less reliable in demanding conditions.
Corrosion Resistance Performance
Epoxy resin in FRP coatings offers excellent corrosion resistance, significantly outperforming traditional coatings. Traditional spray coatings, with their high ester bond content, have lower resistance to corrosive elements, limiting their long-term durability.
Curing Performance
FRP coatings incorporate pre-mixed photocuring agents, allowing for light curing. This ensures a uniform, controlled, and traceable curing process. In contrast, traditional spray coatings require heat curing with manual measurements, which can lead to inconsistencies and traceability issues.
Environmental Protection and Safety
FRP coatings are non-toxic and do not release flammable gases, ensuring a safer working environment. Conversely, traditional spray coatings contain toxic and flammable chemicals, increasing the risk of health hazards and flash explosions.
Material Modulation
FRP coatings maintain a uniform thickness and remain unaffected by climate and environmental changes. Traditional spray coatings require proportional mixing, which depends on environmental conditions, making quality control more challenging.
Welding Line and Seam Treatment
FRP coatings provide a soft, flexible covering that easily and uniformly coats seams, reducing the risk of weak spots. Traditional spray coatings require multiple spray applications, which can result in uneven coverage and potential failure points.
Construction Remediation
Post-construction defects are easier to repair with FRP coatings, ensuring long-term durability. Traditional spray coatings, however, are difficult to repair, and achieving uniform quality after remediation remains a challenge.
Coating Quality
FRP coatings provide a consistent, uniform thickness without pinholes, foreign objects, or sagging. In contrast, traditional spray coatings are prone to uneven thickness, pinholes, and other defects that can affect their overall performance and lifespan.
Conclusion
FRP coatings offer superior performance in nearly every aspect compared to traditional spray coatings. From enhanced adhesion and corrosion resistance to safer application and better curing performance, FRP coatings are a reliable and high-quality solution for industrial coating needs. By choosing FRP coatings, industries can ensure greater durability, efficiency, and safety while reducing maintenance and environmental risks.